Behind the scenes: Adrian Newey’s reveal at Aston Martin’s stunning £200m F1 factory
An exclusive look behind the scenes as Adrian Newey is unveiled at Aston Martin's stunning new £200m F1 factory.
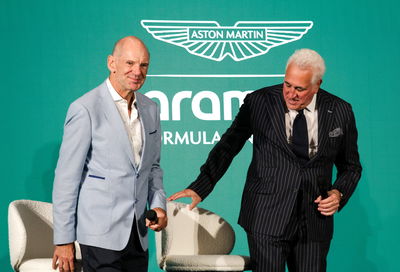
Adrian Newey’s contract announcement brought the F1 world to Silverstone to celebrate the sport’s greatest mind and show off their new toys. Aston Martin’s press conference yesterday marked a seismic shift in the balance of F1.
For them, Newey’s signing represented the dawn of a new era. Their new £200 million, 37,000 sqm factory is now a fortress for the brightest minds in the sport and is fully operational as of this month.
For this writer, the 10th of September 2024 marked a significant career achievement.
An opportunity for the first time to get to the heart of the day’s top story. Amazingly, the invitation to the press conference also included an opportunity to tour the new facility. The whole facility. Not unlike the ‘secret’ tour that Newey himself received back in June.
Newey was right to be impressed by Lawrence Stroll’s work that day, just as Stroll was right to stake his team’s future on the mind of F1’s greatest designer. Enzo Ferrari famously said, “Ask a child to draw a car, and certainly he will draw it red”. When Newey draws a car, he draws a fast one, no matter the colour.
Newey's unveiling
The morning sky above us was just as characteristically British as the Aston Martin brand itself. Two-dimensional and grey, but juxtaposed by the atmosphere of excitement in the building. I collected my badge and was duly escorted upstairs to a media room filled with excited staff and the other invited journalists. It felt somewhat like joining a new school halfway through the year and not knowing where to sit at lunch.

We were escorted down to the new event space to take our seats and set up our tech before the start of the event on the hour. In front of me sat two rows of various senior Aston Martin Lagonda and F1 team staff, all eager to see their new investment unveiled before them. I attached my long lens, hit record on my microphone, and opened the leather Aston Martin Aramco branded notebook that had been left on my chair.
In the notebook went various one-liners and memorable moments. On the topic of the factory and his negotiations with other teams, Newey commented that: “it's not an easy thing to do to build a brand new factory on a greenfield site and bring everybody inside and have a really nice warm, creative feel to it… I’ve seen some new buildings that haven't quite fulfilled that”.
Fernando Alonso described his new managing technical partner as “an inspiration”, with Stroll noting that despite Newey’s monumental salary and equity package “we intend to be around for a very long time together. So, it's relatively inexpensive. For everything, Adrian brings to the partnership”.
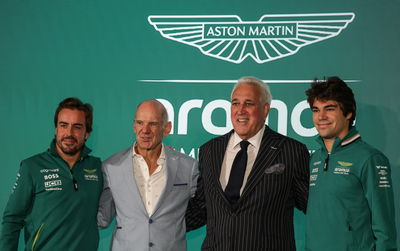
Behind the scenes at Aston Martin HQ
With photos taken and announcement articles finally published, it was the next item on my itinerary that excited me the most about the day. To see behind the scenes of the new facility, guided by a member of the Aston Martin team who knew enough facts and stats about the project to fill an encyclopaedia. Shoutout to Lana.
The project has been built in three phases and over three years and is now essentially fully complete. Before the tour began I was asked politely to put little green Aston Martin branded stickers over my phone camera to prevent any photography of protected IP. This was a sign as good as a sign as any that I would get to see the good stuff.
We began, by design, at the start of the composite manufacturing process. The multidirectional carbon fibre panels, Rohacell foam, and paper-based Nomex honeycomb structures that make up the aerodynamic parts of the car all begin their journey to the racetrack here. From there, the materials are shaped into their forms and taken to huge autoclaves in which they are essentially pressure-cooked and vacuum-sealed.
One can easily imagine that in just over a year’s time when Newey’s first designs are sent through the factory, they will all go through this section of the factory first. I’m told by my guide that facilities of this level represent Aston Martin’s shift to becoming a fully in-house factory team.
We pass composite lamination and head through to composite construction, in which specialised engineers sand down carbon fibre edges in ventilated halls. Next comes Inspection, where the made part is scanned and compared with its original CAD drawing to a 10-micron tolerance - less than the diameter of a single white blood cell.
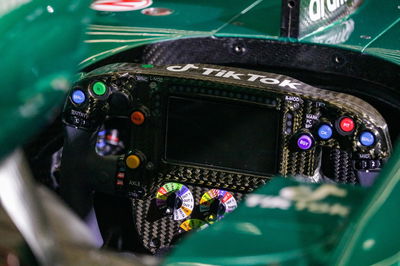
After that, the electronics department. Accurate sensor data is essential in informing the teams and drivers about their performance and tracking car development. I’m told that laid out end-to-end, the wiring of an F1 car would stretch around an entire three-mile lap of the Monaco street circuit.
Electronics also take charge of the steering wheel’s circuitry. 16 buttons, nine rotates, and six rear panels. In a race, those are used 804, 190, and 3000 times respectively on a level that becomes effective automatically to the driver over time.
Non-metallic machining produces roughly 40,000 Rohacell parts per year that are primarily used to construct scale models of the cars for testing. In this section of the building too sits a gargantuan 40-tonne CNC (Computer Numerical Control) machine used to carve out large-scale components from computerised drawings with micron accuracy. As we pass the Metallic Fabrication area I’m handed a “POU bracket’ which forms part of the suspension system and informed that this single component takes over 100 total hours to produce. In other words, don’t drop it.
Finished parts are then quality-controlled to a three-micron tolerance. The non-destructive testing department is finishing its preparation for Baku while the Storage department takes care of organising some 135,000 components, each logged and itemised for later use.
Component Assembly takes these stored parts and, predictably, assembles them into things like the brake pad and disk set I’m handed and told would cost you about £70,000 in material value.
Next are the race bays, one of the highlights of the tour. Up on the stands, with engine cover and front wing removed, sits chassis 22 05. A late-season race car that has been used for young driver testing and will next be driven as a part of a 2026 Pirelli tyre test by F2 Champion and reserve driver Felipe Drugovich.
The lead mechanic working on the car points to various bits and explains, at a level slightly above my understanding, how each part of the engine and cooling components fit together. The engines are so complex and expensive that 1km of running is worth roughly £88.
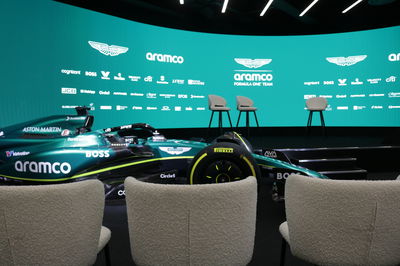
The only part missing from the tour was the design office due to their focus on protected future upgrades which is entirely understandable. However, I was excited by the idea of Newey taking to his drawing board for the first time, in that very room, in March of next year. There’s also an Aston Martin Aramco-branded table football table near the design office.
The race operations room dubbed Mission Control was our next stop. A NASA-style wall of monitors stands in front of rows of computer screens and radio headsets that are used to inform the trackside team on any mid-race strategy ideas. Members of the Aston Martin team are also recruited to monitor the 18 other radio feeds from their competitors to scope out any useful information.
This building also houses the simulator and a huge staff canteen with views over the Buckinghamshire and Oxfordshire countryside. Among our final stops were the paint bays in which the iconic British Racing green, and the logos of all the sponsors that paid for the factory, are added to the car. We then make our way to the crown jewel of the project, and arguably the most significant piece of equipment in the facility, after Newey's new drawing board.
Aston Martin’s wind tunnel features a complex system of laser scanning technology that, at present, they are the only team to have incorporated into the construction of their system, Other teams will be able to retrofit it to theirs, but will be a step behind AM in doing so. The 60% scale models are painted a specific shade of dark red that I’m told best interacts with the laser scanning system. They hang from huge articulating robot arms that hang from the ceiling and are used to transport the models around the space when the time comes to text them. Think Glados from Portal, if you need an image.
An operation room similar to Mission Control monitors the activity of the wind tunnel and analyses the data from some running the previous day. It is in this room that the first signs of Newey’s various technical innovations will be seen. If what I’m told by the team is true, and this wind tunnel works as expected, it is yet another asset that points to a bright future for the team in green.
The wind tunnel marked the crescendo of the tour as I headed back to the media centre to collect my things and head home, repeatedly thanking my tour guide for a truly memorable day. To see F1 at that level of detail was a privilege and something I’ll remember for a very long time. The facility is technically fascinating and architecturally beautiful in equal measure. I got in my car feeling like a very lucky boy, severely out of my depth, who had somehow got away with getting into the cool kid’s party.
Stroll remarked in the press conference: “We all know nothing good is cheap”. A vote of confidence from F1’s greatest designer may be the best evidence yet that their expensive work will soon pay off.
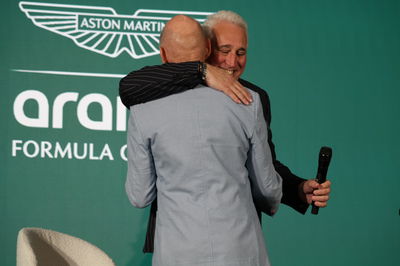